GAS CHARGED SHOCKS, STRUTS, & REPLACEMENT CARTRIDGES
The development of gas charged shock absorbers was a major advance in ride control technology. The advance was to solve ride control problems, which occurred due to an increasing number of vehicles using unibody construction, shorter wheelbases and the increased use of higher tire pressures.
Comfort vs. Control
In the past, ride comfort or vehicle control were compromised by the design limits of conventional hydraulics. A shock absorber or strut can provide either a more comfortable ride or greater vehicle control, but not the optimum of both in the same unit.
A shock or strut damps excessive vehicle spring motion by the controlled movement of fluid under pressure. Fluid provides the resistance to movement and valving controls the amount of that resistance.
Before Monroe gas charged shocks and struts, valve orifices could not be enlarged to increase riding comfort without losing damping effectiveness. So valving was compromised in one of two directions: soft or hard valving.
With soft valving, fluid flows more easily. The result is a smooth ride, but with poor handling – and a lot of roll and sway.
When valving is hard, fluid flows less easily. Handling is improved, but the ride can become rough.
In the past, ride engineers had to choose between soft or hard valving. And, either comfort or control was compromised. In addition, fluid inside the shock absorber could mix with air and turn into foam. Engineers called this aeration. Because foam compresses, the amount of resistance provided by the fluid was hard to predict.
Before the development of Monroe gas charged shocks and struts, other ways to solve these problems had been tried, but had not been totally successful.
The gas cell is one solution. It is a plastic envelope of hexasulphafluoride gas, which is installed between the reserve tube and the pressure tube of a two-stage shock absorber. The gas cell fills the air space to reduce aeration.
High-pressure gas charged shocks are mono-tube shocks, with fluid and gas in separate chambers in most designs. The gas can be charged to 360 psi.
The advanced design of Monroe two-tube gas charged shocks solves many of today’s ride control problems by adding a low-pressure charge of nitrogen gas in the reserve tube. With the shock fluid under pressure, aeration is greatly reduced.
The gas pressure also provides resistance to fluid entering the reserve tube. This, combined with the large piston bore design on Monroe shocks, provides the extra working capacity needed for lower spring rate suspensions.
With Monroe gas charged shocks and struts, you and your customers can enjoy a better ride – plus improved handling.
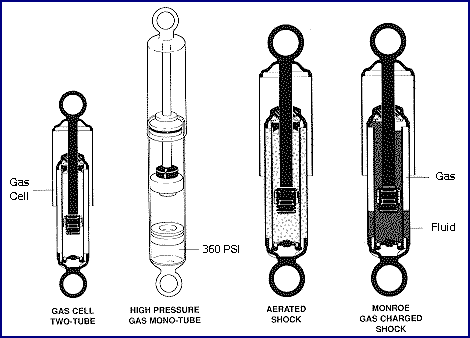
How They Work
The pressure of the nitrogen in the reserve tube of a Monroe gas charged shock varies from 100 to 150 psi, depending on the amount of fluid in the reserve tube. The gas serves several important functions to improve the ride control characteristics of the shock.
One function is to increase the resistance of fluid flow into the reserve tube. This improves valving performance during the compression stroke and also prevents “dumping” into the reserve tube.
Another function is to minimize aeration of the unit’s hydraulic fluid. The pressure of the nitrogen gas prevents air bubbles or foam from weakening the hydraulic effectiveness of fluid flow through both the piston and base valve systems. Foam affects performance – foam compresses, fluid does not.
A third important function of the gas is to allow Monroe engineers greater flexibility in valving design. In the past, such factors as dumping and aeration forced compromises in design.
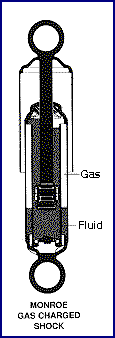